Холодный способ штамповки, предполагающий отсутствие нагрева деформируемой заготовки, является наиболее используемым для получения деталей различной конфигурации. При этом используют специальный инструмент — штамповую оснастку или штамп-форму. В качестве сырья применяется листовой прокат, цветные металлы, а также неметаллическое сырье. Для каждого вида заготовок предполагается специфический метод обработки основных деталей штамп-формы.
Основные этапы изготовления штампов
Изготовление штамп-формы — длительный и трудоёмкий процесс, предполагающий прохождение нескольких этапов:
- формирование заготовок;
- механизированная обработка полученных заготовок;
- процесс слесарной обработки основных элементов (пуансонов, их держателей, матриц, съёмников);
- термообработка деталей;
- механизированное шлифование;
- доводка и ручная шлифовка;
- сборка цельного инструмента, тестирование и отладка.
Особенности выбора метода термообработки деталей холодноштамповой оснастки
Практически все штампы проходят обязательную процедуру термообработки. Но бывают и исключения в виде пренебрежения закалки пуансона при получении изделий исключительно из мягкого сырья (латуни, алюминия). Закалка одной матрицы также положительно сказывается на её сроке службы, так как более мягкий пуансон при люфте не может её деформировать. А при изготовлении вырубных штампов, напротив, требуется более твёрдый пуансон и менее закаленная матрица, тем самым удастся получить на выходе детали с точными наружными размерами.
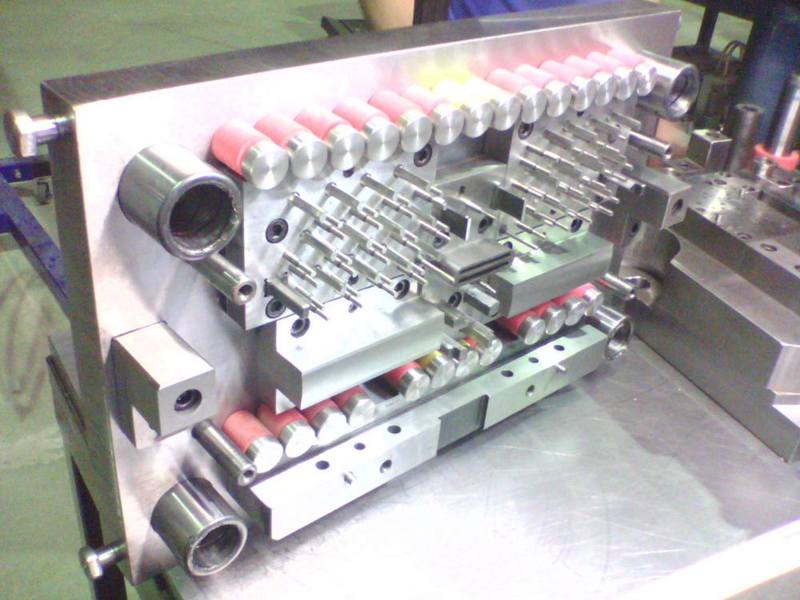
Процесс повышения прочности деталей напрямую зависит от конфигурации, размера и исходного материала:
- маленькие и тонкие пуансоны — отпуск производится вертикальным погружением в масло, допустимо использование воды, при этом узкое ребро должно смотреть вниз;
- толстые и круглые — отпуск режущей кромкой вперед;
- сложной конфигурации и высокой твёрдости — отпуск в масле (60°C) или воде (40°C-50°C) с медленным погружением;
- крупные матрицы с отверстиями — брызговое закаливание исключительно рабочей поверхности;
- пробивные пуансоны большой массы — нагрев в муфельной или электропечи с отпуском в воде, обязательно вертикально, процесс должен проходить одновременно (без полного охлаждения);
- простая форма пуансона — 15-20 мм от лезвия охлаждают в воде, а потом целиком окунают в масло (достигается высокий показатель вязкости сердцевины и хвостовика, а также твердость рабочей поверхности);
- тонкие продолговатые пуансоны — закаливание проходит одновременно по всей длине (для повышения упругости), с отпуском хвостовой части в масле, соляном растворе или нагретом песке;
- короткие пуансоны большой массы — перед медленной процедурой закалки подвергаются отжигу (760-780°C) (для предотвращения появление трещин), охлаждение проводиться из опрыскивателя водой и отпуск в горячем песке или электрической печи;
- детали из легированной стали — сквозная закалка с охлаждением в масле (без перерыва);
- элементы из углеродистой стали — ступенчатая закалка (быстрое охлаждение сначала в солевом растворе, потом в 40°C масле).
Необходимость закалки и выбор технологии термической обработки может определить только высококвалифицированный сотрудник, имеющий опыт подобных работ.
|